It is important to understand the level of purity that is needed for each application in order to purposefully generate your own nitrogen. Nonetheless, there are some general requirements regarding the intake air. The compressed air has to be clean and dry before entering the nitrogen generator, as this positively affects the nitrogen quality and also prevents the CMS from being damaged by moisture. Furthermore, the inlet temperature and pressure should be controlled between 10 and 25 degrees C, while keeping the pressure between 4 and 13 bar. To treat the air properly, there should be a dryer between the compressor and the generator. If the intake air is generated by an oil lubricated compressor, you should also install an oil coalescing and carbon filter to get rid of any impurities prior to the compressed air reaching the nitrogen generator. There are pressure, temperature and pressure dew pointsensors installed in most generators as a fail-safe, preventing contaminated air from entering the PSA system and damaging its components.
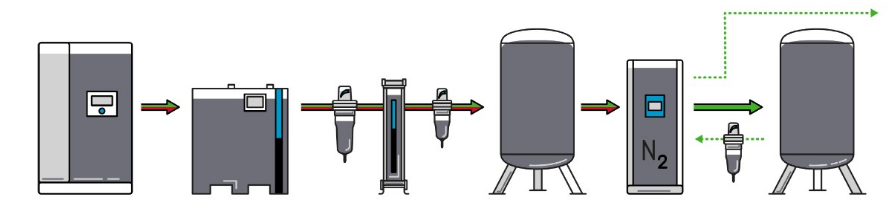
A typical installation: Air compressor, dryer, filters, air receiver, nitrogen generator, nitrogen receiver. The nitrogen can be consumed directly from the generator or through an additional buffer tank (not shown).
Another important aspect in PSA nitrogen generation is the air factor. It is one of the most important parameters in a nitrogen generator system, as it defines the compressed air required to obtain a certain nitrogen flow. The air factor thus indicates a generator’s efficiency, meaning a lower air factor indicates a higher efficiency and of course lower overall running costs.